Interface IO-Link indépendante du fabricant pour l'automatisation intelligente des processus
Introduction
Actuellement, le thème de l'industrie 4.0 et des concepts de machines innovants fait l'objet de nombreuses discussions dans le domaine de l'automatisation. Les conditions de base pour une mise en réseau continue, une transparence totale et une communication sans faille des systèmes d'analyse jusqu'au niveau le plus bas des appareils de terrain sont des capteurs intelligents. Avec l'interface IO-Link, un nouveau concept de communication indépendant du bus de terrain et indépendant du fabricant a été créé pour relier de manière uniforme les capteurs et les actionneurs au niveau de commande à l'aide d'une connexion point à point simple et économique. Le rapport suivant présente la technologie et l'application de l'interface IO-Link.
Industrie 4.0
L'industrie 4.0 est la fusion de la technologie de l'information (TI) et de la technologie des télécommunications pour former la TIC. La base est la mise en réseau des capteurs, des actionneurs et du traitement des données pour une communication continue jusqu'au niveau des appareils de terrain. La vision de l'industrie 4.0 englobe la numérisation, l'automatisation et la mise en réseau de toutes les applications pour le contrôle de l'ensemble du processus pour toutes les fonctions, tous les domaines et tous les segments de l'industrie de fabrication jusqu'à l'action économique. Cette transformation est principalement motivée par les exigences croissantes des clients ou par la nécessité pour les entreprises de fabrication de pouvoir répondre aux souhaits de plus en plus rapides, dynamiques et individualisés des clients. Cela nécessite le passage de systèmes de contrôle de production centralisés et rigides à une intelligence décentralisée jusqu'au niveau des appareils de terrain.
L'introduction de l'industrie 4.0 dans les processus de production doit permettre une fabrication adaptative et une optimisation des différents processus en temps réel. En fonction des techniques de production et de processus définies, les matériaux et les composants doivent être sélectionnés de manière autonome et une adaptation et un réajustement en temps réel doivent être possibles selon la devise "Le produit commande l'installation". Les avantages sont une augmentation de l'efficacité et de la flexibilité grâce à une réaction plus rapide à une plus grande diversité de variantes, des cycles de changement plus courts pour les produits complexes, la fabrication de différentes séries ou de produits individuels avec la même installation, des produits individualisés et adaptés aux clients ainsi que la production de petites et de très petites séries à des coûts compétitifs.
Avec l'industrie 4.0, on passe d'une maintenance préventive des installations à des diagnostics prévisibles et à une maintenance à distance, même au-delà des limites de l'usine et des sites. Tout cela exige l'accès aux sources de données intelligentes connectées, telles que les capteurs ou les actionneurs.
L'une des lacunes de l'industrie 4.0 est l'absence fréquente de norme et la délimitation imprécise du terme. La continuité inter-systèmes et donc la capacité d'utilisation à l'échelle mondiale nécessitent des conditions-cadres uniformes pour les technologies, les systèmes et les processus sur la base de normes et de standards internationaux. À cela s'ajoutent les uniformisations fondamentales des principes de structuration, des interfaces et des formats de données.
L'introduction de l'industrie 4.0 dans les processus de production doit permettre une fabrication adaptative et une optimisation des différents processus en temps réel. En fonction des techniques de production et de processus définies, les matériaux et les composants doivent être sélectionnés de manière autonome et une adaptation et un réajustement en temps réel doivent être possibles selon la devise "Le produit commande l'installation". Les avantages sont une augmentation de l'efficacité et de la flexibilité grâce à une réaction plus rapide à une plus grande diversité de variantes, des cycles de changement plus courts pour les produits complexes, la fabrication de différentes séries ou de produits individuels avec la même installation, des produits individualisés et adaptés aux clients ainsi que la production de petites et de très petites séries à des coûts compétitifs.
Avec l'industrie 4.0, on passe d'une maintenance préventive des installations à des diagnostics prévisibles et à une maintenance à distance, même au-delà des limites de l'usine et des sites. Tout cela exige l'accès aux sources de données intelligentes connectées, telles que les capteurs ou les actionneurs.
L'une des lacunes de l'industrie 4.0 est l'absence fréquente de norme et la délimitation imprécise du terme. La continuité inter-systèmes et donc la capacité d'utilisation à l'échelle mondiale nécessitent des conditions-cadres uniformes pour les technologies, les systèmes et les processus sur la base de normes et de standards internationaux. À cela s'ajoutent les uniformisations fondamentales des principes de structuration, des interfaces et des formats de données.
Les limites de la technologie d'automatisation classique
Jusqu'à présent, les mises en réseau et les systèmes de bus de terrain ont été développés par les principaux fabricants d'API, qui prennent en charge une technologie spécifique au système et sont parfaitement adaptés à leurs outils de programmation et de configuration. Il existe ainsi plusieurs systèmes concurrents sur le marché, comme Profibus/ProfiNet (Siemens),DeviceNet et ControlNet (Rockwell Automation), Modbus et CANopen (Schneider Electric), Interbus (Phoenix Contact) ou CC-Link (Mitsubishi Electric). Le type d'API utilisé détermine quel bus de terrain est utilisé. Les principales différences techniques concernent la longueur du câble, le nombre de bits de données et les fonctionnalités. Des fonctions plus avancées comme le diagnostic, la transmission acyclique des données de demande, la gestion des alarmes et le trafic transversal entre les différents participants au bus ne sont pas supportées par tous les systèmes de bus de terrain.
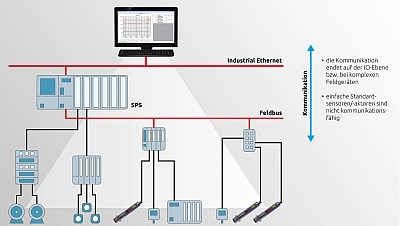
Abb. 1 Système d'automatisation classique à capacité de communication limitée.
Dans la technique d'automatisation classique, la communication s'arrête jusqu'à présent au niveau le plus bas du bus de terrain, c'est-à-dire au niveau des capteurs et des actionneurs (figure 1). On y utilise souvent des modules non communicants qui se limitent à des signaux d'entrée et de sortie purement analogiques ou de commutation. Les capteurs et actionneurs disponibles sur le marché avec une interface numérique ne sont pas normalisés, mais utilisent du matériel et des logiciels spécifiques à l'entreprise pour communiquer. Pour l'installation, il faut, selon le capteur, utiliser des modules spéciaux et coûteux dans la commande. Le câblage hétérogène avec des types de câbles et des affectations de raccordement très différents entraîne des frais d'installation élevés. Pour garantir l'immunité aux interférences des signaux tant analogiques que numériques, il est nécessaire de prendre des mesures importantes en matière de blindage. Dans la pratique, on constate régulièrement que les perturbations lors de la transmission des signaux sont souvent dues à un blindage défectueux ou insuffisant. La mise en réseau et l'intégration des diverses interfaces et protocoles de transmission sont également complexes et sujettes à erreurs. Lors d'un changement de machine, d'un remplacement ou d'un contrôle des appareils, les paramètres doivent être réglés manuellement sur l'appareil ou directement pour chaque capteur et actionneur via un outil séparé. Comme on le constate régulièrement, il s'agit là d'une source importante d'erreurs et de manipulations pour le fonctionnement sûr des installations. Comme il n'y a pas de communication continue du niveau de l'appareil de terrain avec les niveaux supérieurs, les données de diagnostic des capteurs et des actionneurs ne sont pas disponibles. Or, ce sont souvent ces modules qui, en raison de leur positionnement dans l'installation et de leur utilisation dans des conditions de production industrielle difficiles telles que la chaleur, le froid, les vibrations, la saleté et l'humidité, sont responsables des arrêts de l'installation en tant que source d'erreurs. Sans données de diagnostic, la recherche et l'élimination des erreurs s'avèrent souvent difficiles et longues. Il n'est même pas possible de penser à une maintenance préventive pour éviter les temps d'arrêt imprévus.
L'avenir s'appelle IO-Link
Une offre aussi diversifiée de systèmes de bus et l'absence de normes constituent plutôt un inconvénient majeur pour le développement de la technologie d'automatisation. Les fabricants de produits d'automatisation ont dû s'en rendre compte. C'est pourquoi les principaux fournisseurs se sont réunis en consortium dans le but de développer une technologie d'interface E/S généralement valable et standardisée au niveau mondial pour la communication des capteurs et des actionneurs. Il en est résulté le concept IO-Link pour la connexion uniforme, indépendante des bus de terrain et des fabricants, des appareils de commutation et des capteurs au niveau de commande au moyen d'une connexion point à point peu coûteuse. Ce standard de communication est défini dans la norme CEI 61131-9. Les dispositifs IO-Link assurent la transparence et la communication continue du niveau des appareils de terrain jusqu'au niveau supérieur de l'automatisation (figure 2). En tant qu'interface ouverte, IO-Link s'intègre dans tous les systèmes de bus de terrain et d'automatisation courants. Avec IO-Link, seule la transmission numérique doit finalement être utilisée au lieu de l'utilisation parallèle actuelle de signaux analogiques, de commutation et numériques. IO-Link offre la possibilité d'un diagnostic et d'une localisation centralisés des erreurs jusqu'au niveau des actionneurs/capteurs. Grâce à la possibilité de paramétrer dynamiquement les capteurs à partir de la commande de l'installation, les appareils de terrain peuvent être réglés pendant le fonctionnement en fonction des exigences de production. Les appareils de terrain avec interface IO-Link constituent ainsi la base de la mise en œuvre de l'industrie 4.0.
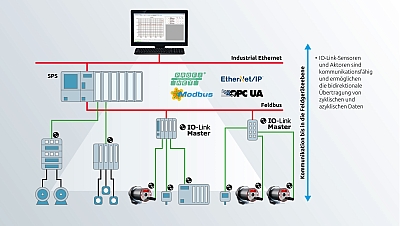
Abb. 2 IO-Link permet la communication de bout en bout jusqu'au niveau de l'appareil de terrain.
Avantages de l'interface IO-Link
L'interface IO-Link est certainement considérée à juste titre comme l'interface USB de la technique d'automatisation. Toutes deux sont des connexions sérielles point à point peu coûteuses pour la transmission de signaux et se prêtent à un fonctionnement plug-and-play. Une caractéristique essentielle est le câblage très simple au moyen de câbles standardisés avec un raccordement par connecteur vissable. Outre l'énorme gain de temps lors du câblage grâce à la suppression des borniers, la solution à connecteur évite la source d'erreur d'une connexion incorrecte et inappropriée. La suppression des câbles multipolaires séparés pour la transmission des signaux analogiques, le contact de commutation et le paramétrage externe réduit le câblage et l'encombrement dans l'armoire électrique, car il n'est plus nécessaire de raccorder chaque appareil séparément à la périphérie centrale. La standardisation inter-constructeurs réduit la diversité des interfaces des capteurs et des modules IO ainsi que les différents câbles de connexion.
Les capteurs avec une interface IO-Link offrent une possibilité de diagnostic fiable. Les messages de diagnostic, en particulier les messages d'état préventifs, peuvent être transmis avec leur description et affichés sur l'IHM (interface homme-machine). Ainsi, en cas de défaillance d'un capteur, d'encrassement d'un capteur optique, de température de fonctionnement inadmissible, de rupture de fil ou de court-circuit, il est possible de réagir rapidement et d'éviter des temps d'arrêt prolongés.
Si un remplacement de capteur s'avère néanmoins nécessaire, une grande source d'erreur réside jusqu'à présent dans le paramétrage correct ou même dans l'utilisation d'un mauvais capteur. Sur les appareils IO-Link, les paramètres sont enregistrés dans le maître IO-Link. Avec IO-Link, une identification des appareils a lieu grâce aux numéros de série, Vendor et Device ID uniques, ce qui exclut toute confusion entre les appareils. En cas de remplacement d'un appareil, les paramètres sont en outre automatiquement transmis au capteur. Toute erreur de manipulation, voire toute manipulation, est ainsi exclue. De plus, les modifications de paramètres peuvent être documentées et donc suivies ultérieurement.
La transmission des données IO-Link est basée sur un signal 24 V et est donc particulièrement insensible aux perturbations électromagnétiques. Comme la transmission des signaux est purement numérique et sécurisée par des sommes de contrôle, les transmissions erronées et les imprécisions dues aux conversions de signaux sont exclues, comme c'est le cas pour les signaux analogiques. Des lignes blindées et des mesures de mise à la terre particulières ne sont généralement pas nécessaires.
Les capteurs avec une interface IO-Link offrent une possibilité de diagnostic fiable. Les messages de diagnostic, en particulier les messages d'état préventifs, peuvent être transmis avec leur description et affichés sur l'IHM (interface homme-machine). Ainsi, en cas de défaillance d'un capteur, d'encrassement d'un capteur optique, de température de fonctionnement inadmissible, de rupture de fil ou de court-circuit, il est possible de réagir rapidement et d'éviter des temps d'arrêt prolongés.
Si un remplacement de capteur s'avère néanmoins nécessaire, une grande source d'erreur réside jusqu'à présent dans le paramétrage correct ou même dans l'utilisation d'un mauvais capteur. Sur les appareils IO-Link, les paramètres sont enregistrés dans le maître IO-Link. Avec IO-Link, une identification des appareils a lieu grâce aux numéros de série, Vendor et Device ID uniques, ce qui exclut toute confusion entre les appareils. En cas de remplacement d'un appareil, les paramètres sont en outre automatiquement transmis au capteur. Toute erreur de manipulation, voire toute manipulation, est ainsi exclue. De plus, les modifications de paramètres peuvent être documentées et donc suivies ultérieurement.
La transmission des données IO-Link est basée sur un signal 24 V et est donc particulièrement insensible aux perturbations électromagnétiques. Comme la transmission des signaux est purement numérique et sécurisée par des sommes de contrôle, les transmissions erronées et les imprécisions dues aux conversions de signaux sont exclues, comme c'est le cas pour les signaux analogiques. Des lignes blindées et des mesures de mise à la terre particulières ne sont généralement pas nécessaires.
Composants du système IO-Link
Un système IO-Link se compose de maîtres IO-Link servant de passerelle entre les systèmes de communication supérieurs tels que Profinet, Ethernet/IP et les dispositifs IO-Link. Les dispositifs IO-Link sont les appareils de terrain capables de communiquer, comme par exemple les capteurs, les appareils de commutation, les vannes ou les voyants de signalisation.
La transmission des données par IO-Link s'effectue en principe entre un maître IO-Link et le dispositif IO-Link en tant qu'esclave. Des modules d'interface pour bus de terrain et des modules d'interface pour API sont disponibles en tant que maîtres IO-Link. Il est possible de faire fonctionner les appareils de commutation comme auparavant, comme une entrée ou une sortie de commutation, ou de transmettre numériquement l'état de commutation en mode de fonctionnement IO-Link. Comme les deux signaux sont transmis par la même broche 4, un fonctionnement en parallèle est exclu. Dans un système IO-Link, les composants avec et sans IO-Link peuvent être combinés à volonté et fonctionner en parallèle. Les appareils standard non compatibles IO-Link peuvent être connectés soit via des ports IO standard spéciaux, soit via les ports IO-Link compatibles du maître. Des capteurs binaires ou analogiques peuvent ainsi être reliés au niveau du bus de terrain via le maître. La compatibilité descendante des ports IO-Link est assurée par le module d'interface IO-Link grâce à deux modes de fonctionnement différents : le mode IO-Link et le mode IO standard (SIO). Les capteurs IO-Link peuvent être utilisés comme un appareil binaire. Ainsi, un capteur de commutation IO-Link peut également être intégré dans des solutions d'automatisation classiques. Lors de l'initialisation, le maître IO-Link établit automatiquement une communication. Un fonctionnement mixte de capteurs standard et de capteurs IO-Link est supporté par le standard IO-Link.
Avec IO-Link, la ligne pour le signal de commutation est utilisée en même temps pour la communication sérielle. Techniquement, il s'agit d'une interface semi-duplex où l'envoi et la réception des données se font l'un après l'autre. Des connecteurs M12 sont utilisés en standard. La longueur maximale du câble jusqu'au maître IO-Link est de 20 m.
La transmission des données par IO-Link s'effectue en principe entre un maître IO-Link et le dispositif IO-Link en tant qu'esclave. Des modules d'interface pour bus de terrain et des modules d'interface pour API sont disponibles en tant que maîtres IO-Link. Il est possible de faire fonctionner les appareils de commutation comme auparavant, comme une entrée ou une sortie de commutation, ou de transmettre numériquement l'état de commutation en mode de fonctionnement IO-Link. Comme les deux signaux sont transmis par la même broche 4, un fonctionnement en parallèle est exclu. Dans un système IO-Link, les composants avec et sans IO-Link peuvent être combinés à volonté et fonctionner en parallèle. Les appareils standard non compatibles IO-Link peuvent être connectés soit via des ports IO standard spéciaux, soit via les ports IO-Link compatibles du maître. Des capteurs binaires ou analogiques peuvent ainsi être reliés au niveau du bus de terrain via le maître. La compatibilité descendante des ports IO-Link est assurée par le module d'interface IO-Link grâce à deux modes de fonctionnement différents : le mode IO-Link et le mode IO standard (SIO). Les capteurs IO-Link peuvent être utilisés comme un appareil binaire. Ainsi, un capteur de commutation IO-Link peut également être intégré dans des solutions d'automatisation classiques. Lors de l'initialisation, le maître IO-Link établit automatiquement une communication. Un fonctionnement mixte de capteurs standard et de capteurs IO-Link est supporté par le standard IO-Link.
Avec IO-Link, la ligne pour le signal de commutation est utilisée en même temps pour la communication sérielle. Techniquement, il s'agit d'une interface semi-duplex où l'envoi et la réception des données se font l'un après l'autre. Des connecteurs M12 sont utilisés en standard. La longueur maximale du câble jusqu'au maître IO-Link est de 20 m.
Dans la première phase du concept de spécification de l'interface IO-Link, l'accent était mis sur les capteurs et actionneurs à commutation. Entre-temps, il a été reconnu que l'utilisation de l'interface IO-Link était également judicieuse pour les appareils de mesure. De plus en plus de fabricants de capteurs proposent déjà des appareils pour diverses grandeurs de mesure physiques. Dans la spécification IO-Link, seules les broches 1, 3 et 4 sont définies de manière fixe, conformément à l'affectation des connexions Port Class A. Les broches 2 et 5, qui sont utilisées si nécessaire pour une alimentation en tension supplémentaire en cas de besoin accru en courant, peuvent être utilisées alternativement pour la sortie analogique 0/4-20 mA ou pour une deuxième sortie de commutation sur les appareils de mesure (figure 3).
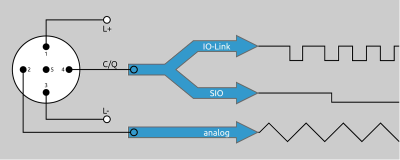
Fig. 3 Connexion d'un capteur moderne avec interface IO-Link et sortie analogique.
Tant que les utilisateurs ne souhaitent pas encore renoncer complètement à la sortie analogique, le fonctionnement en parallèle de la sortie analogique, de la sortie de commutation et de l'interface numérique offre des possibilités intéressantes de paramétrage externe, d'évaluation des messages d'erreur et de fonctions de signal de diagnostic. Si, plus tard, la commande est convertie à une transmission purement numérique des valeurs de mesure, l'effort se limite uniquement à la modification de la configuration du logiciel de commande. Les appareils de mesure, comme par exemple les thermomètres infrarouges pour la mesure de température sans contact, doivent traiter des signaux très faibles de l'ordre du pico-ampère. Cela exige un niveau élevé de mesures internes de protection contre les interférences ainsi que des mesures externes comme l'utilisation d'un câble blindé. Certes, le consortium IO-Link fait de la publicité pour le fait qu'une ligne blindée n'est pas nécessaire pour le raccordement des appareils IO-Link, car les signaux numériques ne peuvent pas être perturbés. Avec l'introduction de l'interface IO-Link dans les appareils de mesure, certaines restrictions sont inévitables. Le marché a d'ailleurs déjà réagi en proposant des câbles confectionnés avec un blindage.
Types de données de la communication IO-Link
La communication IO-Link supporte la transmission de données cycliques et acycliques. Les données de processus et les informations d'état sur la validité des données de processus sont transmises de manière cyclique. Les données des appareils telles que les données d'identification, les paramètres et les informations de diagnostic sont échangées de manière acyclique sur demande du maître IO-Link. En outre, les événements tels que les messages d'erreur (court-circuit, interruption) ou les messages d'avertissement (encrassement, surchauffe) sont signalés par un appareil au maître.
Intégration d'appareils IO-Link dans la commande
Afin d'uniformiser l'accès du programme utilisateur de l'automate aux appareils, des profils d'appareil sont définis pour IO-Link. La structure des données, le contenu des données et la fonctionnalité de base y sont définis. On obtient ainsi un accès identique au programme de l'automate. Le profil d'appareil "Smart Sensor Profil" est défini pour IO-Link.
Le fichier de description d'appareil IODD (IO Device Description) est un composant d'un appareil IO-Link. La structure de l'IODD est la même pour tous les appareils de tous les fabricants. La même manipulation est ainsi garantie pour tous les appareils IO-Link, indépendamment du fabricant. Il contient toutes les informations et les textes descriptifs concernant l'identification, les paramètres de l'appareil avec les plages de valeurs, les messages d'erreur, les données de processus et de diagnostic ainsi que les propriétés de communication (figure 4). Les textes peuvent être enregistrés en plusieurs langues. Les ports des appareils connectés sont attribués dans le maître IO-Link (image 5). Le maître IO-Link est alors généralement couplé à la commande en tant qu'esclave de bus de terrain.
Le fichier de description d'appareil IODD (IO Device Description) est un composant d'un appareil IO-Link. La structure de l'IODD est la même pour tous les appareils de tous les fabricants. La même manipulation est ainsi garantie pour tous les appareils IO-Link, indépendamment du fabricant. Il contient toutes les informations et les textes descriptifs concernant l'identification, les paramètres de l'appareil avec les plages de valeurs, les messages d'erreur, les données de processus et de diagnostic ainsi que les propriétés de communication (figure 4). Les textes peuvent être enregistrés en plusieurs langues. Les ports des appareils connectés sont attribués dans le maître IO-Link (image 5). Le maître IO-Link est alors généralement couplé à la commande en tant qu'esclave de bus de terrain.
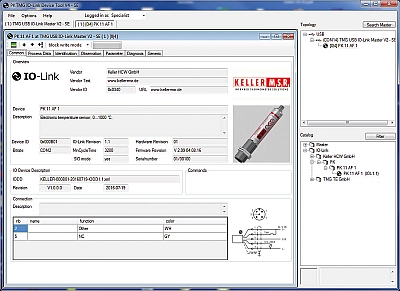
Fig. 4 Propriétés du dispositif d'E/S connecté.

Fig. 5 Intégration d'un capteur IO dans le maître.
Le paramétrage et le diagnostic sont effectués automatiquement par un bloc fonctionnel dans la commande de la machine. Lors du paramétrage, le bloc fonctionnel demande d'abord les paramètres d'identification des appareils raccordés via IO-Link. Ensuite, il vérifie par comparaison avec la base de données si ces capteurs sont autorisés pour les machines. Si c'est le cas, le bloc fonctionnel trouve également dans la base de données les paramètres de configuration correspondant aux capteurs. Si nécessaire, ceux-ci sont alors automatiquement écrits dans les capteurs respectifs via IO-Link. Par exemple, pour le pyromètre (figure 6), il est possible de paramétrer l'émissivité, les points de commutation et la fonction du contact de commutation, la mise à l'échelle de la sortie analogique et la mémoire de valeur maximale.
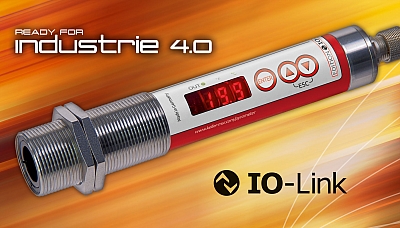
Abb. 6 Pyromètre avec interface IO-Link, sortie analogique et contact de commutation.
En outre, une simulation de température, un autotest et une réinitialisation aux réglages d'usine sont possibles en tant que fonctions de commande (figure 7). Les erreurs dans le matériel ou le logiciel, les demandes de maintenance ou le fonctionnement de l'appareil en dehors des spécifications peuvent être évalués entre autres par la fonction de diagnostic. Avec l'intégration dans le système de commande, les capteurs sont également accessibles pour une maintenance à distance.
Le paramétrage spécifique à l'utilisateur d'un appareil IO-Link peut être effectué en externe de trois manières : via un PC avec un maître IO-Link USB, via un outil logiciel dans l'automate ou de manière programmée par des blocs fonctionnels de la commande de l'installation.
Le paramétrage spécifique à l'utilisateur d'un appareil IO-Link peut être effectué en externe de trois manières : via un PC avec un maître IO-Link USB, via un outil logiciel dans l'automate ou de manière programmée par des blocs fonctionnels de la commande de l'installation.
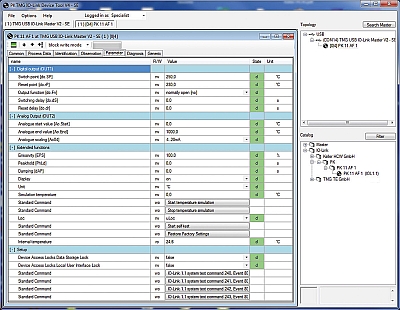
Abb. 7 Réglage des paramètres et des commandes
Outils IO-Link pour le service
Un ancien responsable de la mise en service argumentera certainement qu'il était jusqu'à présent beaucoup plus simple de contrôler un capteur analogique au moyen d'un appareil de mesure de courant. Le paramétrage pouvait être réglé à l'aide d'un bouton-poussoir ou d'un commutateur sur l'appareil. Mais si l'on doit alors renoncer aux autres avantages de la communication numérique, on peut se demander si cela peut encore être un argument décisif d'achat dans la concurrence internationale pour l'optimisation des coûts de production.
Des maîtres USB IO-Link sont proposés pour le service (image 8). Ils permettent d'exploiter un appareil IO-Link via un PC par interface USB. Des adaptateurs IO-Link spéciaux peuvent être insérés dans le câble d'alimentation afin de pouvoir accéder aux données et les enregistrer sans rétroaction par câble ou sans fil via Bluetooth. Des adaptateurs sont également disponibles pour cloner les paramètres de l'appareil.
Des maîtres USB IO-Link sont proposés pour le service (image 8). Ils permettent d'exploiter un appareil IO-Link via un PC par interface USB. Des adaptateurs IO-Link spéciaux peuvent être insérés dans le câble d'alimentation afin de pouvoir accéder aux données et les enregistrer sans rétroaction par câble ou sans fil via Bluetooth. Des adaptateurs sont également disponibles pour cloner les paramètres de l'appareil.
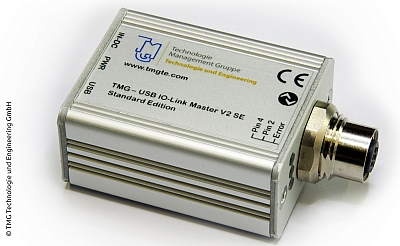
Abb. 8 IO-Link Master pour le raccordement d'un IO-Link Device ü à un PC via l'interface USB.
La rapidité du passage à une communication des signaux purement numérique n'est pas prévisible et dépend certainement étroitement du degré d'automatisation des machines, de l'industrie et des applications. Comme les capteurs modernes avec interface IO-Link et sortie analogique sont souvent proposés sans supplément de prix, il est recommandé d'utiliser ces appareils en prévision d'un remplacement, d'une extension de l'installation ou même d'une nouvelle installation. Un changement ultérieur est ainsi très simple et possible sans frais de transformation des capteurs et du câblage.
Plus de 3000 produits IO-Link sont déjà proposés. Des maîtres IO-Link sont désormais disponibles pour 16 systèmes de bus de terrain. De plus, 8 fabricants de systèmes de commande proposent déjà des maîtres centraux. S'y ajoutent de nombreux fabricants de capteurs pour les grandeurs de mesure les plus diverses, pour la reconnaissance d'objets ou la détection de positions, ainsi que des actionneurs comme des voyants de signalisation, des vannes, des contacteurs de puissance ou des convertisseurs de fréquence. Diverses entreprises proposent également la technologie pour la conception d'appareils et l'assistance technique. L'obligation de certification et l'utilisation d'outils de test accrédités garantissent que tous les produits disponibles sur le marché sont conformes à la norme IO-Link.
Plus de 3000 produits IO-Link sont déjà proposés. Des maîtres IO-Link sont désormais disponibles pour 16 systèmes de bus de terrain. De plus, 8 fabricants de systèmes de commande proposent déjà des maîtres centraux. S'y ajoutent de nombreux fabricants de capteurs pour les grandeurs de mesure les plus diverses, pour la reconnaissance d'objets ou la détection de positions, ainsi que des actionneurs comme des voyants de signalisation, des vannes, des contacteurs de puissance ou des convertisseurs de fréquence. Diverses entreprises proposent également la technologie pour la conception d'appareils et l'assistance technique. L'obligation de certification et l'utilisation d'outils de test accrédités garantissent que tous les produits disponibles sur le marché sont conformes à la norme IO-Link.