Prinzip, Vorteile und Einsatzmöglichkeiten von neuartigen Panorama-Pyrometern
Einleitung
Temperaturmessung von bewegten Objekten
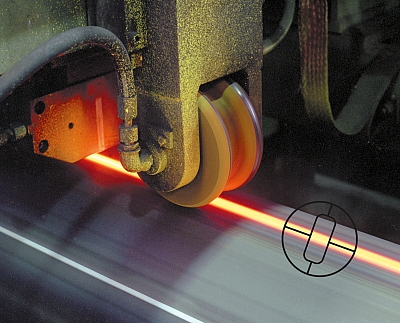
Abb. 1 Solange der Draht innerhalb des Messfeldes schwingt, ist eine korrekte Messung möglich.
Daher hat es schon vor vielen Jahren Versuche mit Geräten gegeben, die ein rechteckförmiges Messfeld auf rein optischer Weise erzeugten. Eine spezielle Zylinderlinse spreizte dabei das Messfeld in Richtung einer Achse, wie man es aus einem Spiegelkabinett kennt. Grundsätzlich konnte damit eine Lösung geschaffen werden. Als ein Problem erwies sich die ungleichmäßige Empfindlichkeitsverteilung auf der Messfläche des Sensors. Nachteilig waren zudem die hohen Kosten dieser Speziallinse. Außerdem waren die Geräte nur für einen festen Messabstand einsetzbar. Eine weitere Schwierigkeit war, dass das optische Bild im Durchblickvisier verzerrt und daher das Gerät schwer auszurichten war.
Interessant ist die Verwendung eines rechteckigen Messfeldes insbesondere in Verbindung mit einem Quotienten-Pyrometer. Ein Quotienten-Pyrometer erfasst die Wärmestrahlung eines Messobjektes in zwei unterschiedlichen Wellenlängenbereichen. Der Quotient der beiden spektralen Strahldichten ändert sich proportional zur Temperatur. Dieses Messprinzip ermöglicht es, dass das Messobjekt auch kleiner als das Messfeld sein darf. Im Unterschied zu einem Einkanal-Pyrometer wird bei einem heißen Messobjekt vor einem kalten Hintergrund dennoch die richtige Temperatur ermittelt.
Aufbau und Funktionsweise
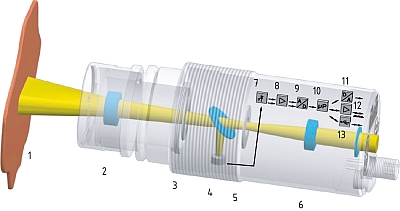
Abb. 2 Blockbild des optischen Aufbaus des Panorama-Pyrometers: Messobjekt (1), fokussierbares Wechselobjektiv (2), Blendensystem (3), Umlenkspiegel und Sensor (4), Messfeldmarkierung (5), Okular bzw. Videokamera(6)
Eine weitere optische Herausforderung war bei der Entwicklung des Panorama-Pyrometers zu lösen. Durch optische Abbildungsfehler und eine inhomogene Empfindlichkeitsverteilung auf der Messfläche haben Quotienten-Pyrometer üblicherweise die Eigenschaft, dass die Position des Messobjektes im Messfeld einen merkbaren Einfluss auf die gemessene Temperatur hat. Im Randbereich des Messfeldes kann bei einer Objekttemperatur von 1000 °C die Anzeige um über 30 °C ansteigen (Bild 3).
Auch kann es bei herkömmlichen Quotienten-Pyrometern zu Schwankungen in der Temperaturanzeige kommen, wenn sich der Durchmesser des Messobjektes produktionsbedingt ändert und damit das Messfeld unterschiedlich ausgefüllt ist.
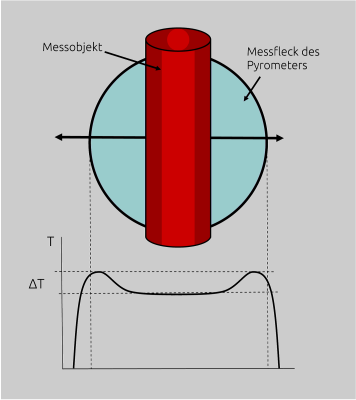
Abb. 3 Fehlerhafter Temperaturanstieg bei Quotienten-Pyrometern, wenn sich das heiße Objekt im Randbereich des Messfelds befindet.
Vielfältige optische Variationsmöglichkeiten
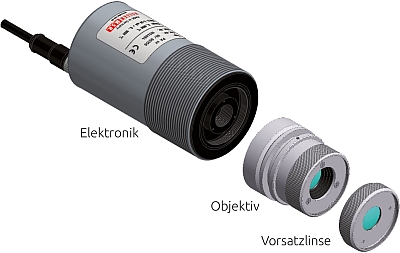
Abb. 4 Modularer Aufbau des Pyrometers bestehend aus Elektronik, Wechselobjektiven und optionaler Vorsatzlinsen.
Einfache Ausrichtung und hohe Betriebssicherheit
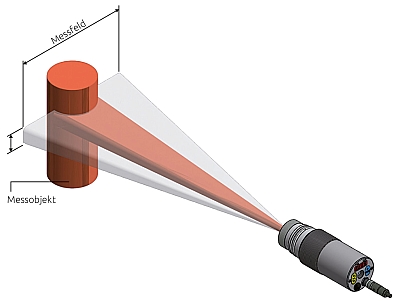
Abb. 5 Die Ausrichtung des Panorama-Pyrometers mit rechteckigem Messfeld auf kleine Objekte und große Messabstände ist denkbar einfach.
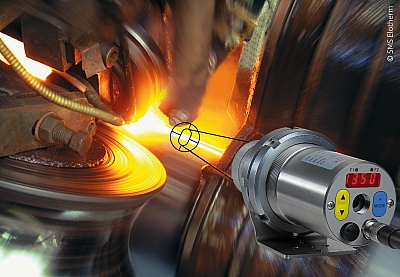
Abb. 6 Sichere Temperaturmessung auch bei schwankender Position der Schweißnaht.
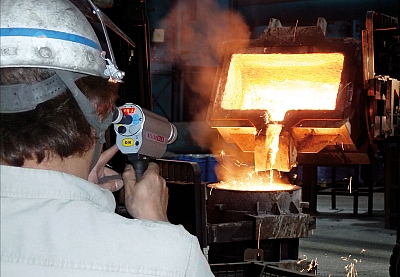
Abb. 7 Messung der Temperatur beim Gießen mittels eines tragbaren Panorama-Pyrometers.
Typische Anwendungsbereiche
Ein typisches Beispiel ist die Produktion von Endlosrohren, in denen das Material gebogen und zusammen geschweißt wird. Die Aufheizung erfolgt per Induktionsspule. Die Position der kleinen Schweißstelle kann schwanken, so dass bei herkömmlichen Geräten die Schweißnaht auch mal außerhalb des Messfeldes liegen könnte und dann keine Messung mehr möglich ist (Bild 6).
Bei der Produktion von Glasflaschen ändert sich die Position und Form des Glastropfens an der Schere. Auch hier liefert ein Panorama-Pyrometer eine höhere Messsicherheit. Hinzu kommt noch Temperatureinfluss des Materials und der Farbe des teils transparenten Glases. Dieser Einfluss wird durch das Quotienten-Messverfahrens des Panorama-Pyrometers stark vermindert.
In Drahtziehanlagen wird der Draht einer anschließenden Wärmebehandlung unterzogen. Dabei läuft der Draht mit hoher Geschwindigkeit durch eine Induktionsspule hindurch. Zwischen den Führungsrollen ist ein Schwingen des Drahtes unvermeidbar. Bei dünnen Drähten kann die Schwankungsbereite schon einmal das Mehrfache des Drahtdurchmessers betragen. Eine punktuelle Messung ist unter diesen Bedingungen kaum noch möglich.
Die manuelle berührungslose Temperaturmessung von flüssigem Metall beim Gießen in die Form erfolgt aus sicherer Entfernung. Mit einem herkömmlichen Gerät mit rundem Messfeld ist es schwierig, das Pyrometer auf den Gießstrahl auszurichten, zumal sich die Position des Strahles je nach Kippwinkel der Pfanne ändern kann. Ein Gerät mit rechteckigem Messfeld ist hierbei wesentlich einfacher zu handhaben (Bild 7).
Die Temperaturmessung kleinster Objekte wie etwa eine Glühwendel oder ein Heizelement in einer Röntgenröhre stellen schon höchste optische Ansprüche an die Geräte. Großteils waren derartige Anwendungen bislang nur mit sogenannten Intensitätsvergleichspyrometern lösbar. Bei den Geräten erfolgt die Temperaturerfassung manuell durch einen visuellen Abgleich der Strahldichte eines geräteinternen Referenzstrahlers und des Messobjektes durch den Bediener.
Die Schwierigkeit bei Verwendung elektronisch messender Geräte lag in der mechanischen Ausrichtbarkeit der Geräte auf extrem kleine Messobjekte. Auch derartige Messaufgaben lassen sich mit dem Panorama-Pyrometer wesentlich einfacher lösen.
Messtechnische Grenzen
Dieser Wert hängt u.a. vom Emissionsgrad des Messobjektes und der absoluten Temperatur ab. Am Messbereichsanfang kann ein Quotienten-Pyrometer bereits einen zuverlässigen Messwert liefern, wenn die Strahlungsenergie 10 % der Strahldichte eines Schwarzen Strahlers bei gleicher Temperatur beträgt. Mit steigender Messtemperatur ist sogar noch eine größere Signalschwächung zulässig. Zur Schwächung tragen der Emissionsgrad, der Grad der Teilausleuchtung, die Form des Messobjektes und sichtbehindernde Einflüsse wie Dampf, Staub und Rauch im Messfeld bei. Als Beispiel sei ein Stahldraht mit einem Emissionsgrad von 0,6 angenommen. Bei einem runden Messobjekt ist zusätzlich zu berücksichtigen, dass die vom Pyrometer erfasste Strahlung teils unter sehr flachem Winkel abgestrahlt wird. Näherungsweise wird dann noch der Sicherheitsfaktor von 1,5 mit einkalkuliert. Aus den folgenden Formeln lassen sich der Grad der Teilausleuchtung, die Breite des Messfeldes und die maximale Messentfernung berechnen.
Grad der Teilausleuchtung = (minimal auswertbare Signalstärke ÷ Emissionsgrad) × Sicherheitsfaktor
Bezogen auf das obige Beispiel muss das Messfeld mindestens zu 10 % ÷ 0,6 × 1,5 = 25 % ausgefüllt sein, damit das Pyrometer einen Messwert ermitteln kann. Die Signalstärke als Indiz für die Sicherheit des Messwertes lässt sich auf dem Display des Pyrometers anzeigen.
Für einen Drahtdurchmesser von 5 mm ergibt sich daraus für den Messbereichsanfang eine maximale Breite des Messfeldes von 5 mm ÷ 0,25 = 20 mm.
Bei einem Panorama-Pyrometer wird die optische Auflösung durch das Distanzverhältnis (Messabstand ÷ Messfeldgröße) für die Breite DW (width) und für die Höhe DH (height) angegeben. Bezogen auf ein Distanzverhältnis von beispielsweise DW = 40 : 1 ergibt sich eine maximale Messentfernung von 40 × 20 mm = 800 mm. Oder anders betrachtet bei einem vorgesehenen Messabstand von beispielsweise 500 mm ist ein Objektiv mit einem Distanzverhältnis von DW ≥ 500 mm ÷ 20 mm sprich ≥ 25 : 1 einzusetzen, damit das Messfeld vom Messobjekt ausreichend ausgeleuchtet wird.
Das Panorama-Pyrometer kann auch so betrieben werden, dass das Messfeld längs zum Objekt ausgerichtet ist. Damit erfasst das Pyrometer eine größere Fläche vom Messobjekt im Vergleich zu einem Gerät mit rundem Messfeld, so dass es so für Drähte mit einem Durchmesser ab 0,1 mm einsetzen lässt.
Geräteausführungen

Abb. 8 Kompaktes Panorama-Pyrometer mit LED Pilotlicht.