How do we manage this? Only regenerative, i.e. with the help of hydrogen, electrification, biogases or synthetic gases, biogenic porosification agents, with high-temperature storage technology and digitalization.
The KELLER team of experts will be happy to assist you and present forward-looking energy concepts for optimum energy efficiency measures.
Each concept is elaborated on a plant- and customer-specific basis via a process analysis and shows you the best possible savings potential.
We offer you a large range of services for the optimization of process engineering procedures, from raw material analysis to on-site measurement, computer-aided analysis and model calculation.
Furthermore, we show you various possibilities for the use of alternative energy sources.
CO2 neutrality
Our energy concepts for optimal energy efficiency measures
Increasing energy efficiency - energy concepts
The first and essential step towards CO2 neutrality must first be to increase energy efficiency, which ultimately leads to decoupling the kiln and dryer as far as possible. In order to achieve the goals, the following topics must be addressed:
Drying
- Short passage lengths = efficient drying
- Low temperature drying / open-air drying
- Delta T control
- Heat recovery from wet air in combination with a heat pump
Firing
- Targeted wheel cooling
- Improved car joint seals
- Circulation systems in the kiln
- Use of preheated combustion air
- Use of clean gas burners
- Improved insulation on walls, ceilings and cars
- Reduction of exit losses due to light cars and light kiln furniture
- Long cooling zone, long heating zone
- Reduction of air flow rate, lambda control in the firing zone
- Energy recovery from the flue gas
General
- Intelligent control and regulation of energy flows
- Avoidance of compressed air - replacement by electrical energy
- Avoidance of hydraulic systems
- Intelligent and predictive maintenance
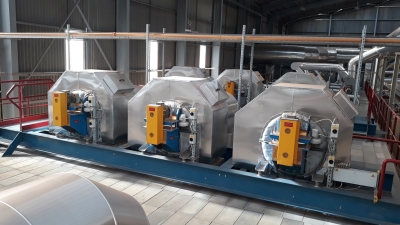
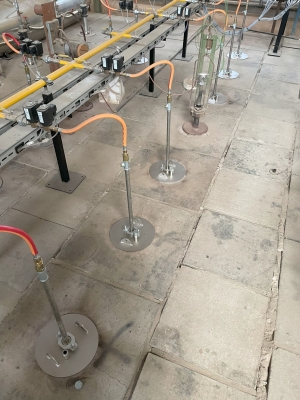
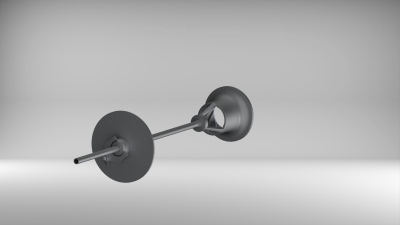
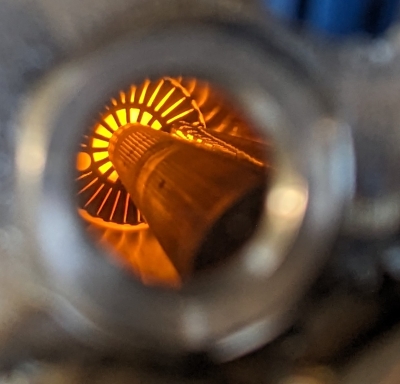
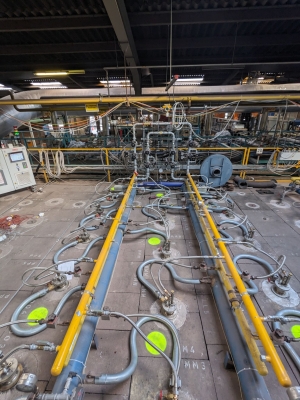
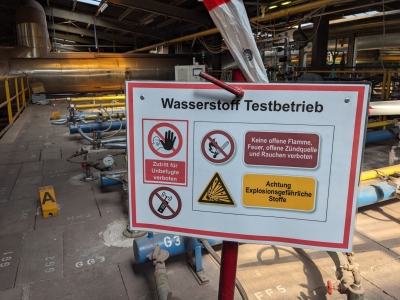
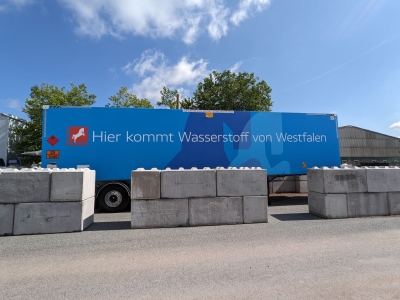
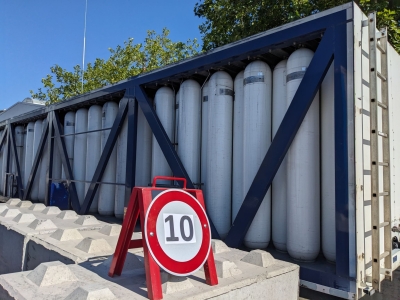
Hydrogen - KELLER successful hydrogen firing test under real operation conditions
KELLER is a member of a research community consisting of several partners from North Rhine-Westphalia: institutes, burner manufacturers, brickmakers and plant manufacturers.
In a three-week test, bricks were produced under real conditions with the addition of hydrogen as fuel. With the new burner technology (dual fuel burner), it is feasible to operate both with 100% H2 and alternately with 100% natural gas.
This positive and pragmatic success places KELLER now in a position to deliver burner technology for hydrogen operation, together with the required control and safety technology. And thus, it fulfils its ambitious goal of increasing energy efficiency for the brick and tile industry and reducing CO2 emissions at the same time.
KELLER will actively follow the hydrogen production and storage possibilities and continue to monitor the improving of the infrastructure in this respect, both in Germany and in Europe.
In a three-week test, bricks were produced under real conditions with the addition of hydrogen as fuel. With the new burner technology (dual fuel burner), it is feasible to operate both with 100% H2 and alternately with 100% natural gas.
This positive and pragmatic success places KELLER now in a position to deliver burner technology for hydrogen operation, together with the required control and safety technology. And thus, it fulfils its ambitious goal of increasing energy efficiency for the brick and tile industry and reducing CO2 emissions at the same time.
KELLER will actively follow the hydrogen production and storage possibilities and continue to monitor the improving of the infrastructure in this respect, both in Germany and in Europe.
Electrification - Our experience and assessments
We see different possibilities for electrification.
Electrification possibilities for drying and firing
- Metallic resistance heater for an annealing temperature of max. 1,150 °C
- Ceramic resistance heater for an annealing temperature of max. 1,500 °C
- Induction heating
- Hot air generators are being developed with the aim of achieving an output temperature of 1,500 °C - resistance heater, induction, microwave
- Use of heat pumps
- High-temperature heat accumulator to compensate for discontinuous production processes and to store "green energy"
- In addition to drying and firing, other process steps can also be electrified - for example an all-electric film hood machine
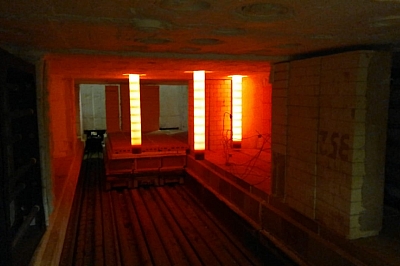
Electric heating rods in the KELLER test kiln