The Energy Efficiency Act § 17 EnEfG has been in force in Germany since 1 January 2024 with the aim of increasing energy efficiency and reducing energy consumption throughout Germany.
According to the EnEfG, all commercial enterprises with an annual energy consumption of more than 2.5 GWh/a must provide information on their waste heat for the first time by 30 June 2024. The data must be up-to-date and reported annually in future.
In a brick plant, this includes at least the amount of flue gas at the tunnel kiln, the wet air from the drying system and the excess kiln air that is blown off. These energy flows can be determined directly in the pipework or, in the case of structurally difficult arrangements, via differential measurements before and after the blow-off point. The measured values can be recorded and analysed in the KELLER K-Matic system or processed with other data loggers and process control systems.
This is proven and reliable industrial measurement technology that can be used not only for quantity determination but also for process optimization.
We will be happy to perform an audit in your plant, make recommendations for the correct selection and positioning of the measuring devices and provide you with a quotation.
We also offer oxygen measurements in pipework or in the kiln, additional temperature sensors or humidity measuring devices.
Measuring technology for waste heat measurements
According to the Energy Efficiency Act - § 17 EnEfG
Schematic view: measurement of waste heat flows
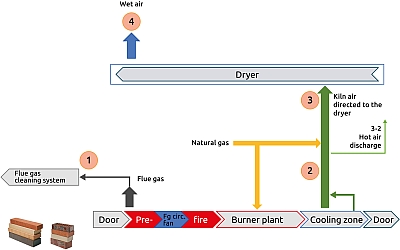
Measuring point | Measuring system Pitot probe | Measuring system Anemometer |
---|---|---|
1 - Flue gas | A/B | |
2 - Kiln air | A | B |
3 - Dryer hot air , hot air blow-off | A | B |
4 - Wet air < 95 % RH | A | B |
Measuring technology for waste heat measurements - our range includes:
Package A: measurements via 1 1/4" pitot probes with temperature measurement
Classic air volume measurement with pitot tube as "point measurement" with assigned temperature measuring point. The flue gas is measured with an improved pitot probe which measures across the whole cross-section. This probe is back-purged with compressed air.
Package B: measurements via high temperature anemometers - 1/2" connection
The air volume measurement via anemometer as "point measurement" provides direct signals with flow velocity in m/s and temperature in °C. The flue gas is measured with an improved pitot probe, which measures across the whole cross-section and is back-purged with compressed air. This solution stands out due to its low installation complexity.
Classic air volume measurement with pitot tube as "point measurement" with assigned temperature measuring point. The flue gas is measured with an improved pitot probe which measures across the whole cross-section. This probe is back-purged with compressed air.
Package B: measurements via high temperature anemometers - 1/2" connection
The air volume measurement via anemometer as "point measurement" provides direct signals with flow velocity in m/s and temperature in °C. The flue gas is measured with an improved pitot probe, which measures across the whole cross-section and is back-purged with compressed air. This solution stands out due to its low installation complexity.
In order to be able to determine the optimum measuring points in your plant, it is necessary to check its structure in advance:
- Is it possible to utilize existing measuring points and integrate them into the waste heat measuring?
- Are there sufficient inlet and outlet pipe runs provided for flow meters?
- How can the acquisition and visualization of the measurement data obtained be integrated into the existing control system and process control technology?