The machinery was replaced starting with the wet side, dry side, setting plant, unloading and packing systems and adapted to the current requirements. The existing tunnel dryer and the tunnel kiln with upright kiln car setting are still being used.
Large-format roof tiles with a demand of 10 pieces per m² are produced in the plant.
The production takes place around the clock and is only interrupted by a maintenance shift during the week.
Roof tiles
References of the ICS business unit can be found here
Further development of a production site in Poland

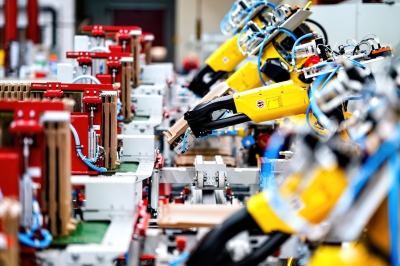
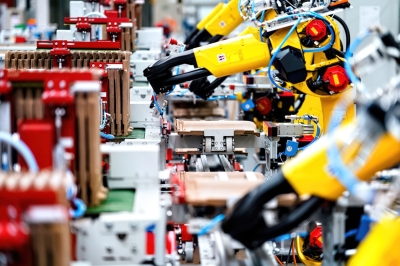
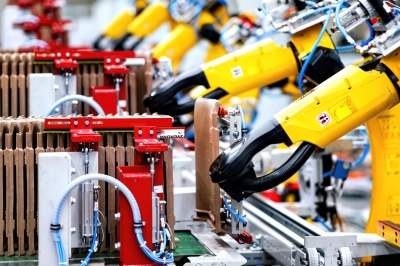

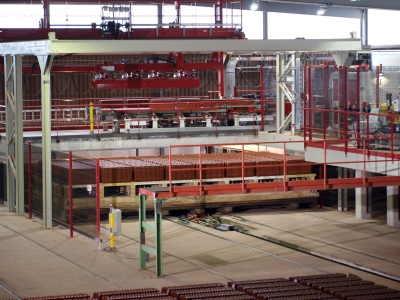
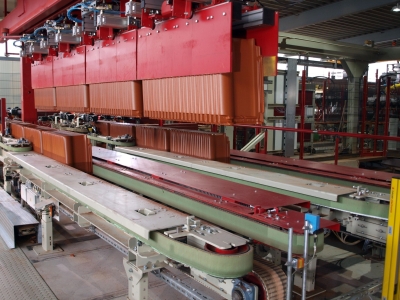
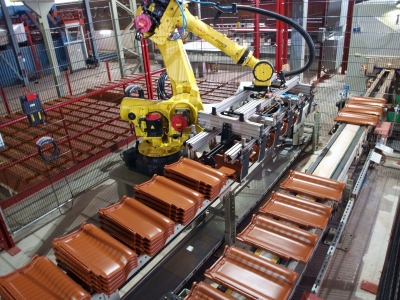
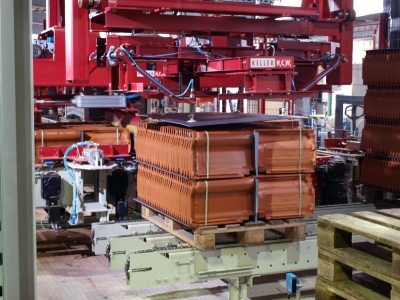
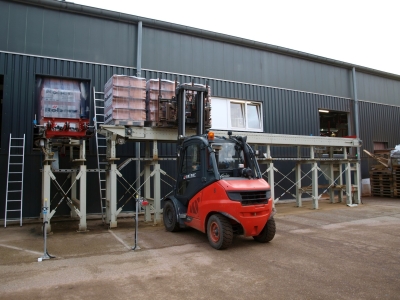
Röben, Brüggen - Quality control at its best
4,300 roof tiles per hour are unloaded from a kiln car with direct setting. The roof tiles are then gripped one by one and turned over to lie on their underside. At defined intervals, they are conveyed to an automatic surface inspection system.
Without any contact, the surfaces of the sensitive roof tiles are then scanned for dimensional accuracy, absence of cracks, shape and surface finish. In fractions of a second, the system decides whether the scanned roof tiles meet the high quality requirements and can be passed on to the packaging station.
Any deviation, no matter how small, from the freely configurable and very tightly set tolerances is registered, archived, and the roof tile in question is sorted out fully automatically.
The inspected and approved roof tiles are put together in small packs and strapped for transport.
Without any contact, the surfaces of the sensitive roof tiles are then scanned for dimensional accuracy, absence of cracks, shape and surface finish. In fractions of a second, the system decides whether the scanned roof tiles meet the high quality requirements and can be passed on to the packaging station.
Any deviation, no matter how small, from the freely configurable and very tightly set tolerances is registered, archived, and the roof tile in question is sorted out fully automatically.
The inspected and approved roof tiles are put together in small packs and strapped for transport.
Dachziegelwerke Nelskamp, Groß Ammensleben - New perspectives in roof tile production
The starting points of the planning were to increase production capacity and introduce new products. The goal was to gradually develop the Groß Ammensleben plant into an efficient and sustainable production site for roof tiles.
In the first step, the accessories plant was extended in 2000. This measure anticipated the demand of flat tile production for accessories for the final extension stage and introduced a new extruded interlocking tile.
In the first step, the accessories plant was extended in 2000. This measure anticipated the demand of flat tile production for accessories for the final extension stage and introduced a new extruded interlocking tile.
The second step and core point of the extensions was the new construction of the second flat tile plant for interlocking tiles.
With the extension of the accessories plant and the new construction of a second flat tile plant, a high-quality and variably expandable product range can be manufactured at the Groß Ammensleben site in the long term.
With the extension of the accessories plant and the new construction of a second flat tile plant, a high-quality and variably expandable product range can be manufactured at the Groß Ammensleben site in the long term.
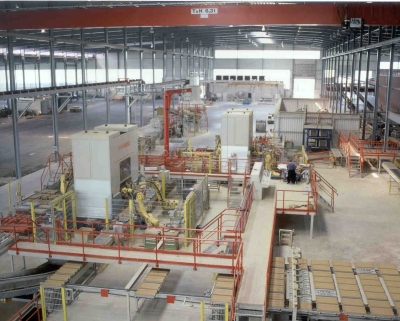
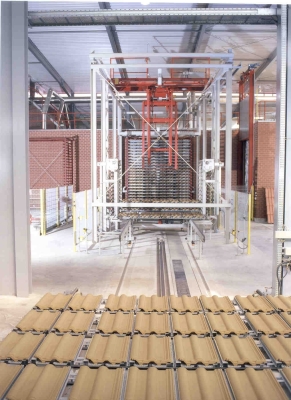
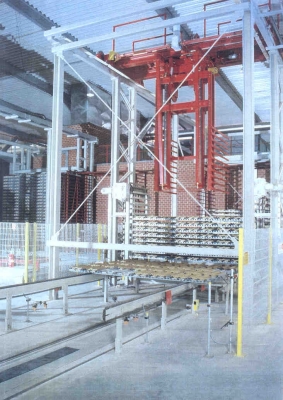
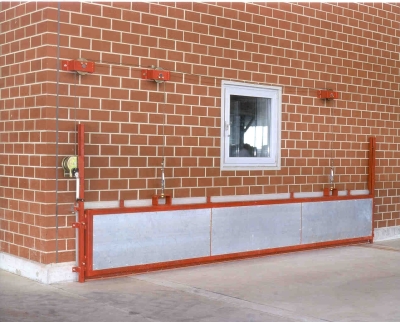
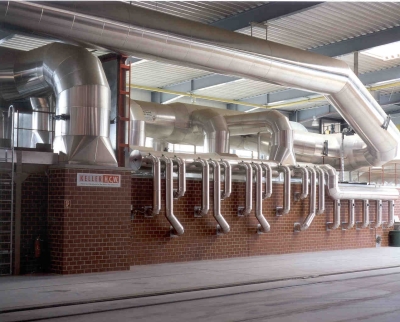
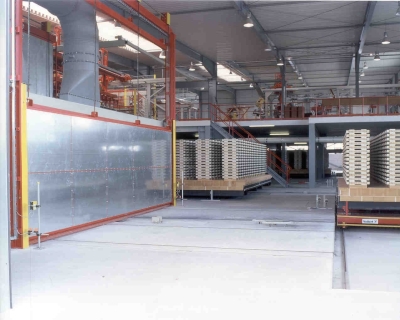
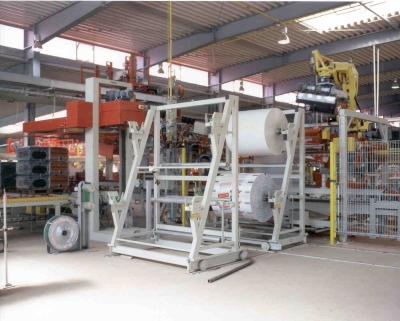